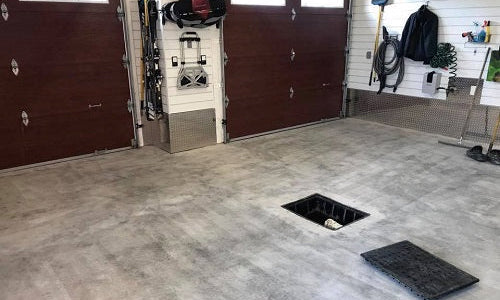
SURFACE PREPARATION GUIDELINES
PowerCOAT Canada has developed this document to help Facility Owners, Architects, Engineers, Specification Writers, and Contractors gain a better understanding of the importance of a properly prepared substrate, and the methods to achieve an appropriate bond. This document is intended to be a general guideline, for specific job site information, please contact your local PowerCOAT Canada Representative.
There are many satisfactory methods of preparing a substrate to receive a PowerCOAT Canada flooring system. The preparation method is typically chosen based on service requirements, time allowed for entire process and accessibility.
PERSONAL PROTECTION EQUIPMENT
It is the responsibility of the surface preparation contractor and the flooring contractor to insure that all personnel are properly protected from hazards. PowerCOAT Canada is committed to promoting awareness regarding these potential hazards. All PowerCOAT Canada products are rated according to the Hazardous Material Identification System (HMIS). OSHA regulations specify when, where and how workers are to be protected. These regulations and the local OSHA officials should be consulted as necessary to insure proper protection, compliance with the law, and to avoid liability issues. Safety and health issues should be addressed prior to the start of the job.
Testing For An Existing Sealer
Test to see if the floor is “sealed” by pouring a small amount of muriatic acid on the floor in several spots. If it “froths” instantly, the floor is not sealed. If the acid doesn’t froth immediately, a sealer and/or paint is present and must be removed by grinding, steel shot blasting or other mechanical methods.
Salt Contamination Testing
Salt contaminated slabs that contain steel reinforcement are very susceptible to corrosion of the reinforcing steel (rebar). As the steel corrodes it expands causing cracking, delamination of concrete and any toppings bonded to it and eventually, structural failure of the slab. Obvious signs of chloride or salt contamination are spalled concrete with exposed, rusted reinforcing steel. Testing is recommended to determine the depth of contamination and the extent of corrosion activity. A Litmus Test for pH will determine the presence of chloride or acid contamination, if the pH is below 10.
REMOVAL AND REPAIR
ASTM D 4258-83 Standard practice for surface cleaning concrete for coating. This practice includes surface cleaning of concrete to remove grease, dirt, and loose material prior to the application of coatings. Procedures include vacuum cleaning, air blast cleaning, water cleaning, detergent water cleaning, and steam cleaning.
Removal of bond inhibiting contaminants
This includes, but is not limited to removal of oils, grease, wax, sealers, curing compounds, laitance, salts and any other hydrocarbon based materials. This will ensure that a good bond takes place between the resinous flooring and the concrete substrate.
Removal of Adhesives, Mastics and Membranes
In many retrofit projects, existing tile, VCT or sheet goods are being replaced with polymer flooring systems. Removal of the floor finish will often leave a layer of some type of mastic, adhesive or membrane. In thin applications these materials can often be totally cleaned up by shotblasting the concrete. In thicker applications, the steel shot will tend to bounce, requiring additional preparation with the use of scarifying equipment or possibly even the use of chemical strippers. Wherever possible, consult the PowerCOAT Canada Tech Service Department or your local PowerCOAT Canada Flooring Contractor and schedule a site visit to investigate the best removal methods.
Removal of Existing Seamless Floor
Like mastics and adhesives, the need to remove an existing seamless floor will occasionally arise. There has been much progress made in the development of equipment for removal of resurfacers. Typically, removal requires a heavy grinder with “rotating heads”. These heads can be outfitted with different “diamond teeth” or carbide “blades” for removal of a particular type of overlay.
REASONS FOR SURFACE PREPARATION
Surface preparation of a concrete substrate is required to remove surface laitance to create a surface profile and porosity for adhesion of polymer floor systems.
METHODS OF SURFACE PREPARATION
Care should be taken to define the degree of abrasion required for the coating system so that the concrete will not be eroded beyond what is necessary. All concrete surfaces should be abraded to remove laitance and contaminants. The following Table describes the required profiles according to the ICRI guidelines for various coating systems.
REASONS FOR SURFACE PREPARATION
Surface preparation of a concrete substrate is required to remove surface laitance to create a surface profile and porosity for adhesion of polymer floor systems.
METHODS OF SURFACE PREPARATION
Care should be taken to define the degree of abrasion required for the coating system so that the concrete will not be eroded beyond what is necessary. All concrete surfaces should be abraded to remove laitance and contaminants. The following Table describes the required profiles according to the ICRI guidelines for various coating systems.
Shotblasting
Shotblasting is the recommended method of surface preparation of concrete for most polymer floor installations. Shotblast equipment utilizes an alloy wheel spinning at high speeds to throw small steel particles at the substrate in a controlled, dry, 99% dust-free operation. This process removes surface contamination, adds profile and vacuums the concrete clean in one process. The size and angularity of shot, along with the travel speed of the unit, can be adjusted to determine the degree of the surface profile. Because shotblasting is a dry preparation process, it allows the installation to begin immediately after completion of prep (surface must be dry before blasting). Shotblasting will also identify weak areas in the surface of the concrete. NOTE: When selecting shotblast preparation for thin film coating systems (under 20 mils) be aware that a blast pattern or track lines may be visible.
Diamond Grinding
Diamond grinding should only be used in areas inaccessible to shotblasting and then only with coarse diamond wheel.
Scarifying
Scarifying is primarily used for the removal of deteriorated concrete, coatings and polymer flooring systems.
Hand Tool
Hand tool preparation consists of the use of mechanical tools and equipment designed to abrade or chip away the surface of the concrete. Common tools available include chipping hammers, hand held diamond grinders and concrete crack chasing saws. These tools are typically used to make keyways, prepare edges against walls and columns.
TYPES OF SUBSTRATES
Regular Concrete
Regular concrete surface must be prepared with a steel shot-blast machine, scarifier or diamond grinder. Floors with oil, grime and grease should first be cleaned with PowerCOAT Industries™ Cleaner/Degreaser before preparing. Allow floor to dry. Good ventilation, fans and/or auxiliary heat will accelerate drying time. Do not use oil fired portable heaters.
Replacement of Structurally Deteriorated Concrete Replacement of structurally deteriorated concrete must be done in accordance with The International Concrete Repair Institute (ICRI) Bulletin. Patching material must be a PowerCOAT Industries™ approved patching material. Make sure of minimum cure time before installation of resinous flooring. PowerCOAT Industries™ flooring Contractors should be contracted whenever possible to complete these repairs appropriately.
Fiber Filled Concrete
Fiber filled concrete must be burned with a propane weed burner, swept and vacuumed perfectly clean and then primed. When primer has completely cured, the floor must be sanded and tack ragged (This step may not be necessary for thick resurfacing systems).
Plywood
The plywood substrate must be sound and non- flexing under the expected load. Typical plywood substrate must be exterior or marine grade, new, clean, and smooth finish (NO KNOTS).
Two layers with staggered joints are required. Plywood should be positively fastened to the existing surface with a high quality construction adhesive as well as a 6” screw pattern.
For further information on plywood substrates, please contact your local sales representative or PowerCOAT Industries™ technical department.
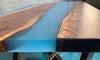
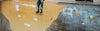